03-08-2022
|
5 min read time
Airsocks at Polyplastic by Lippert
""Vlint is a nice company to work with"
Polyplastic by Lippert, founded in 1952, is European market leader in the production and sale of standardised and customised acrylic window systems. This means that everything from the production of the raw material, acrylic, to the manufacture of individual window systems is all done under one roof.
Since 2020, Rotterdam-based Polyplastic has been part of parent company Lippert, a leading global manufacturer and supplier of high-tech products and customised solutions dedicated to shaping, growing and improving the motorhome, marine, automotive, commercial vehicle and construction products industries.
Essential importance
Air quality in a manufacturing facility where acrylic solutions are produced is essential. It must always be paramount that the production process is safe and hygienic. Ramon Vingerling, Account Manager Industry, at Vlint knows this better than anyone: "We have been supporting Polyplastic for years with solutions that optimise the air quality in the factory and offices to ensure a comfortable and healthy working environment. For example, our experienced service technicians change the filters of the air conditioning units twice a year, we reconditioned the air handling units (AHUs), the AHU's damper registers and frames were replaced and the units were coated. As a result, the AHUs are like new again! We also provide activated carbon changes as an additional service."
Temperature in the factory
Simone van Beest, Team Lead Facility Services at Polyplastic, points out that an additional task was added in the summer: "It was essential for the production process of the screens to lower the temperature in zone 1, the part of the production hall where the screens are produced, by a few degrees. In August, we therefore replaced the air distribution hoses with a new set of hoses for optimal supply and distribution of clean air in this zone."
A plan for optimal cooling
Ramon asked his colleagues at Vlint Air Distribution for advice in this regard. They then examined the airflow in the production hall and wrote a plan for optimal cooling, heating and supply of clean air, applied to the production process of Polyplastic by Lippert. Ramon: "In consultation with Simone and the team at Polyplastic by Lippert, the decision was made to move the excess cooling capacity at the front of the plant to the back using a transport hose to air distribution hoses with a semi-circular shape (D-shape). These have the advantage that the freshly supplied air mixes with the air in the room via the permaebility of the material and the applied perforation. This creates a homogeneous distribution of air. These air distribution hoses were then measured, designed and hung by us in the production hall in August.
Final result
Simone van Beest is satisfied with the end result and happy with the cooperation with Vlint: "It has become a beautiful whole, matching the company's image: clean, light and neutral. We enjoy working with Vlint. Ramon and his colleagues know what they are talking about, give good advice and the fitters work well and neatly. We are satisfied. Vlint is a real partner and a nice company to work with."
That the aforementioned approach was the right one for the temperature in the production hall, Ramon realises when he takes a quick walk to the relevant part of the hall after the interview: "I noticed immediately that it is much cooler in this part of the hall now compared to the old situation." He also gets this confirmation from several employees working in the hall.
“"It has turned out nicely, matching the look of the company: clean, light and neutral. We work with Vlint in a pleasant way."
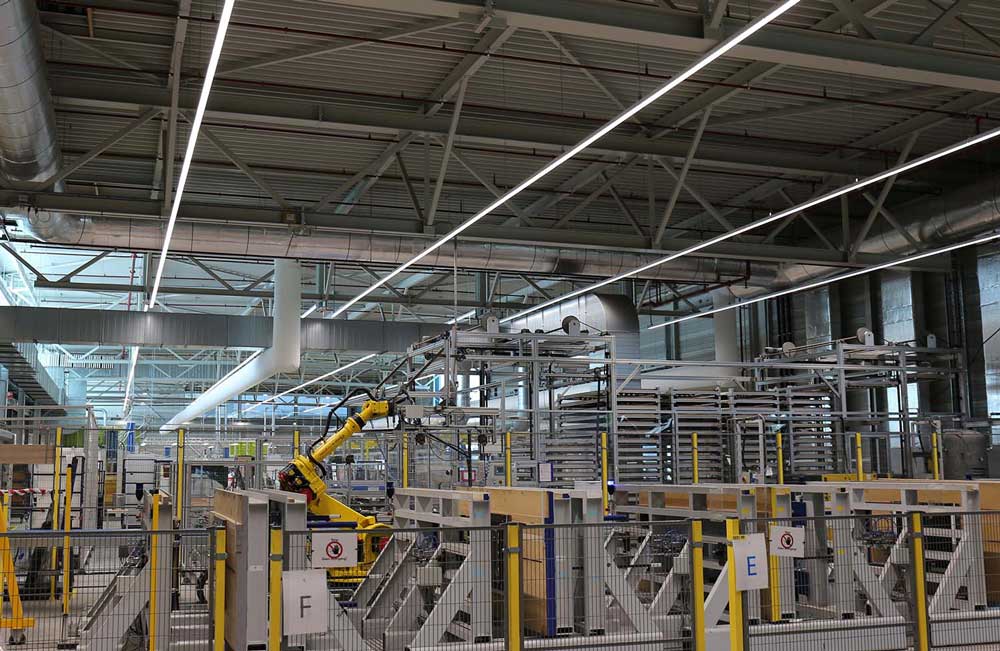
Wondering what we can do for you?
At Vlint, we help our clients by first properly analysing the problem. We then create and implement an effective plan of action to properly solve the problem. In addition, at Vlint, you can count on good after-sales service.
Interested? Get in touch with us