12-07-2022
|
5 min read time
Vlint's 360º total approach at Kerry BV
"Vlint's consultants look beyond others and live up to the 360º approach. A total of six concrete, cost-saving and safety-enhancing solutions have been implemented."
Kerry BV produces emulsifiers in Zwijndrecht. This food product is used by food manufacturers to mix two substances that are normally impossible or difficult to mix. Emulsifiers are found in the production of chocolate, whipped cream and even bread.
Due to the high temperatures and chemicals (e.g. acetic acid) in the production process, high demands are placed on Kerry. Customers of the emulsifiers visit regularly to check that products are made safely and that the production environment is clean.
Vlint has been supporting Kerry for more than nine years with solutions that optimise quality and safety. In doing so, Vlint's technical advisers look beyond others and live up to Vlint's 360º approach in the factory. Vlint has provided a total of six concrete, cost-saving and safety-enhancing solutions
Solution 1: Masterflex hoses for clean and safe design
The first step in the production process of emulsifiers is to mix vegetable oil and various auxiliaries (e.g. catalysts). The hoses that transported these aids at Kerry wore out over time, after which the technical department taped them off. This was to the detriment of the neat appearance in the factory.
Vlint identified which requirements the broken hoses had to meet and introduced Masterflex hoses. These are hoses that can handle constant temperatures of up to 80 degrees, are antistatic, and comply with food legislation. In addition, the hoses have a beautiful appearance, ensuring a 'clean design' in the factory.
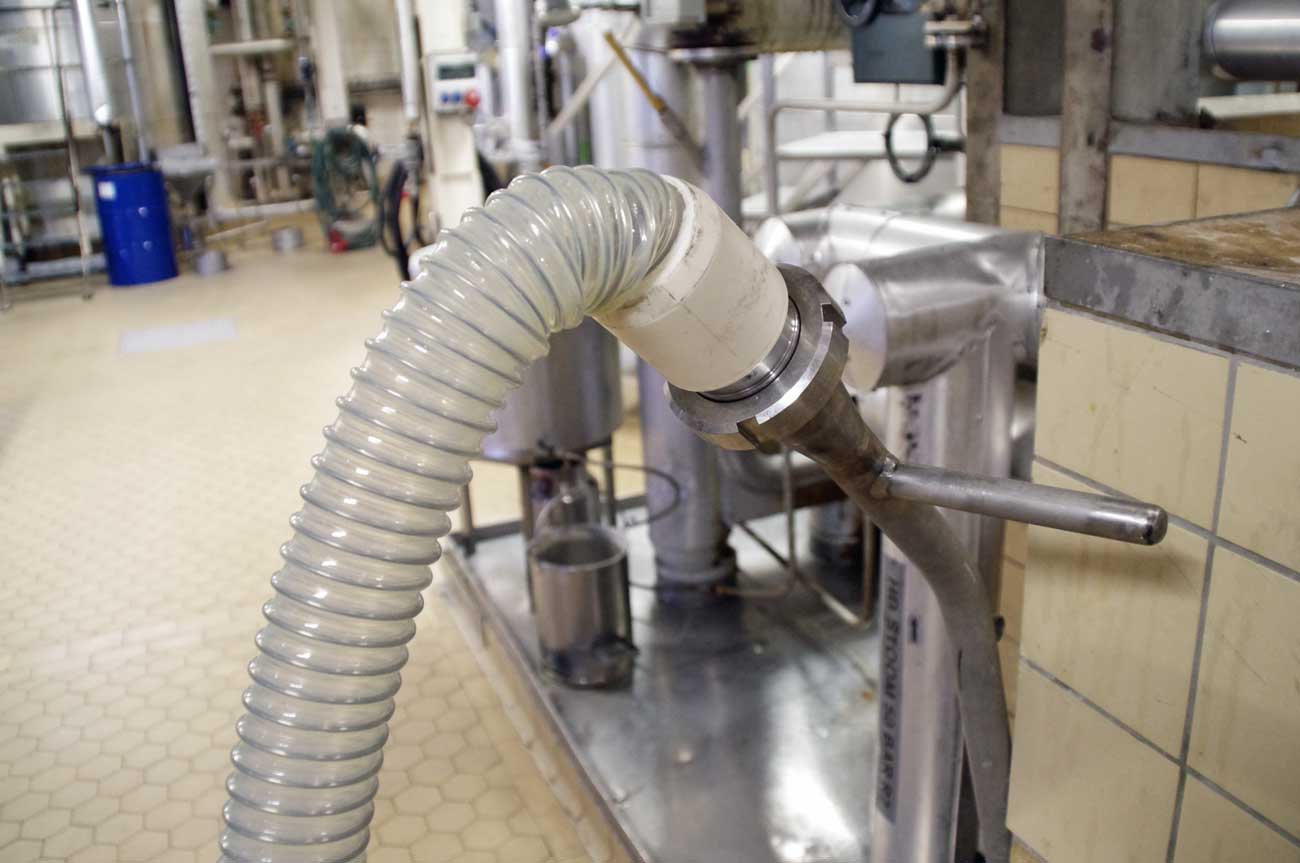
Masterflex indsutriële slangen
|
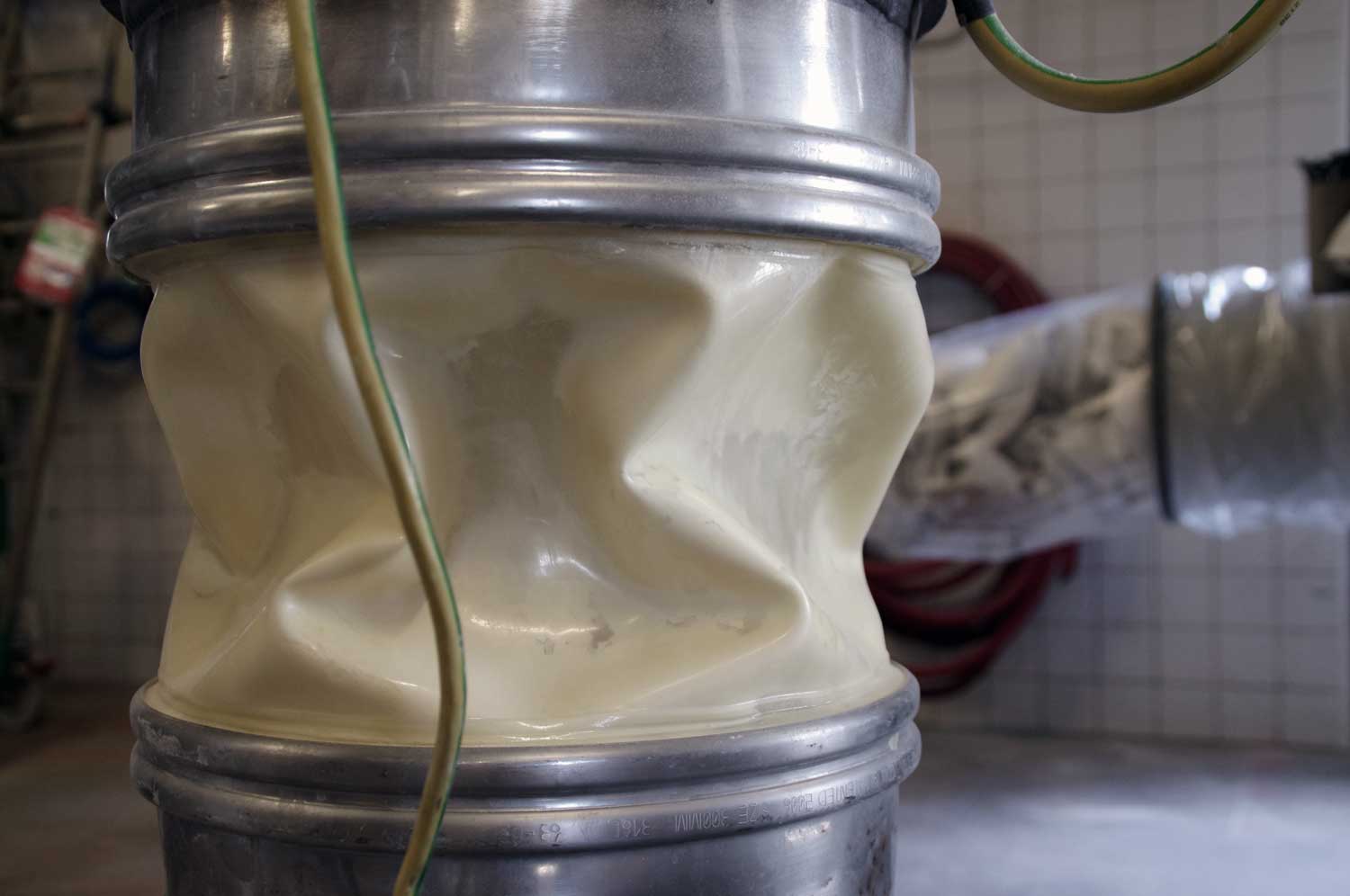
Stofdichte BFM-fittingen
|
Solution 2: dust-tight BFM fittings
Kerry used cuffs to move emulsifier powder. These cuffs were fixed with clamps. In many cases, this caused leaks and contamination in the plant. Like taped hoses, cuffs thus undermined the hygienic appearance expected in the food industry.
The clamped cuffs Vlint replaced with BFM fittings. These cuffs can be clicked between two adapters without the use of tools and meet all the requirements of a food chemical company. Unlike the old cuffs, the BFM fittings are completely dust-tight, so the plant is now no longer contaminated by leaks.
Solution 3: new design filter plant
At one of the dedusting plants linked to the spray towers that made emulsifier powder, excessive emissions occurred. Moreover, the dozens of cartridge filters in the plant only had a service life of a week. This was because the pleats of the cartridge filters quickly filled up with the sticky product in the plant. In addition, the design of the installation was problematic. Because the cartridge filters were horizontal, product fell from the upper filters, onto the filters below.
Vlint concluded that the dedusting plant with cartridge filters needed to be replaced. Vlint's technical experts recommended building a new plant with filter bags. Vlint calculated the required filter area for the new plant, which would significantly increase the filter life. The new plant now only requires preventive filter changes four times a year. This saves Kerry a considerable amount of money.
Solution 4: filters turned inside out
Kerry's dedusting systems contain hundreds of custom-made filter bags. These have to be suitable for ATEX environments and for food production. They have to be very reliable, because the moment the bags tear, Kerry gets contamination in the spray towers. In such a case, the dirt has to be melted down from the tower, which can shut down the factory for up to 24 hours.
To minimise such risks of a production stop and prevent product contamination at all times, Vlint has also made a number of improvements to the filter bags at Kerry. Vlint now supplies bags that are turned inside out, reducing wear and tear on the seams of the filter bags. Moreover, no more stitching can come off, further reducing the risk of product contamination. Also, Vlint has started sewing bags with thread specially selected for application at the Kerry factory.
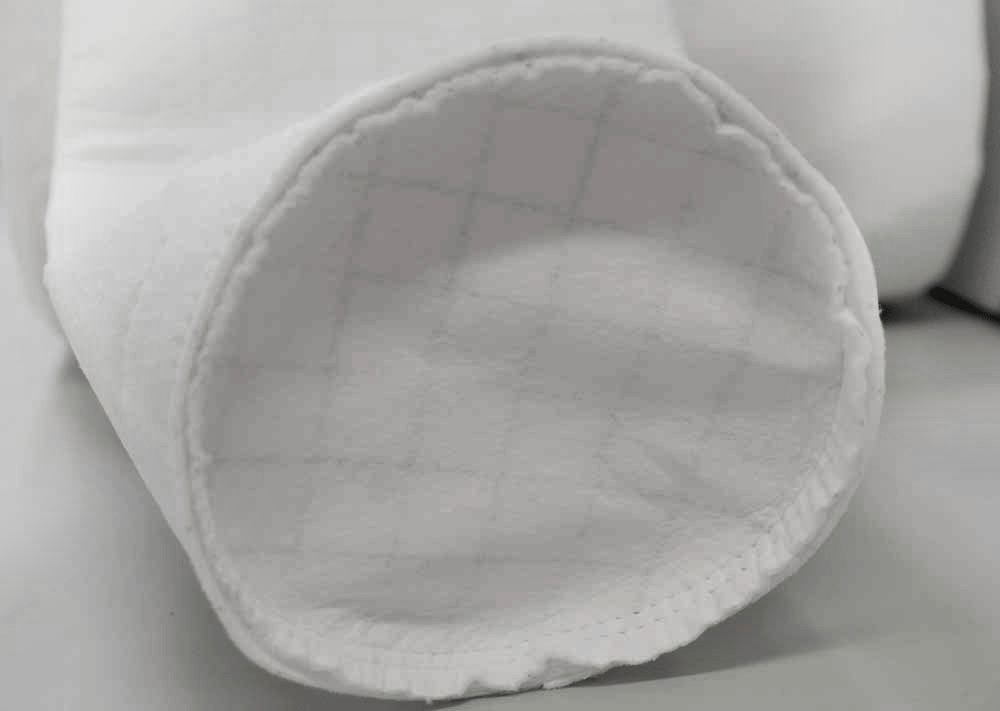
Filterslang met normale bodem
|
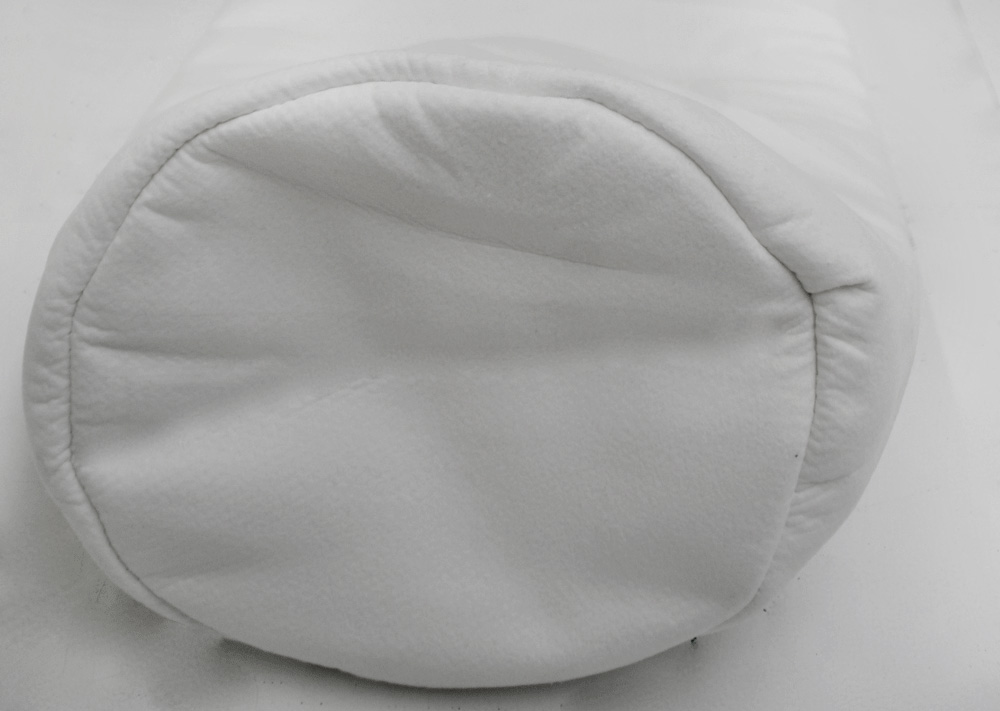
Filterslang met binnenstebuiten gekeerde bodem
|
Solution 5: rapid filter changes by Vlint
At the Kerry site today, there are two large dedusting plants containing hundreds of filter bags. Many of these filter bags are difficult to reach due to the design of the dedusting facilities. Kerry's technical department consists of five people and struggles to carry out the filter changes alongside daily tasks.
Vlint solved this problem by having five specialised mechanics do the job. Because they have years of experience with dedusting plants and do filter changes daily, they can complete the changeover at Kerry within a day. As a result, the plant has hardly any downtime.
Solution 6: repair cladding AHU of lyophilisation unit
The air drawn in by Kerry's spray towers must pass through freeze-drying equipment. This prevents product ingrowth in the spray towers. The cladding of the air handling unit that supplies the freeze drying units with clean air had oxidised on the outside over the years. This created a risk of damage to the sensitive equipment on the inside.
Vlint replaced the cladding of the AHU of the freeze drying plant and provided it with a special coating. This prevents the cladding from rusting through and ensures optimum hygiene in and around the plant.
" "Also, Vlint always has the product certificates neatly in order
and the certificates come from the appropriate notified bodies.""
The result
Ed Verver, Head of Technical Services at Kerry, is delighted with Vlint's 360º approach. 'Via supply of filters, Vlint came in to us, but because Vlint has a very broad market presence, it has been able to help us with many more products. Vlint's filters, cuffs, hoses and coatings have provided even more safety in the factory and a neat appearance of equipment.'’
Besides Vlint's solutions, the head of technical services at Kerry is also satisfied with Vlint's fast service. 'When we ask for information, we get a quick response. Also, Vlint always has the product certificates neatly in order and the certificates come from the right notified bodies. For us, this makes Vlint a pleasant partner to work with.'’
Wondering what we can do for you?
At Vlint, we help our clients by first properly analysing the problem. Then, we create and implement an effective plan of action to properly solve the problem. Interested? Feel free to leave your contact details. We will contact you within one working day.
Please contact me