31-05-2022
|
1 minute read time
Reduced risk of dust explosions at AkzoNobel
The challenge
Polymer powders producer AkzoNobel Elotex in Geleen worked a lot with traditional cuffs. These were not dust-tight, which required extra cleaning work and increased the risk of dust explosions. The AkzoNobel plant had a total of 25 different types of cuffs in circulation. The wide variety of materials meant that the plant's technical department had to pay close attention when changing materials.
The solution
On Vlint's advice, to replace the traditional cuffs, AkzoNobel first installed one BFM fitting on the most problematic connection of the screening machine. As a result, dust leakage stopped at this location and the explosion risk was significantly reduced.
The fitting performed so well that AkzoNobel later fitted all 25 types of connections at the plant with BFM fittings. In the process, all connections were standardised by fitting BFM adapters in various places. The standardisation saves the technical department a lot of work and prevents leaks due to assembly errors or wrong sizing.
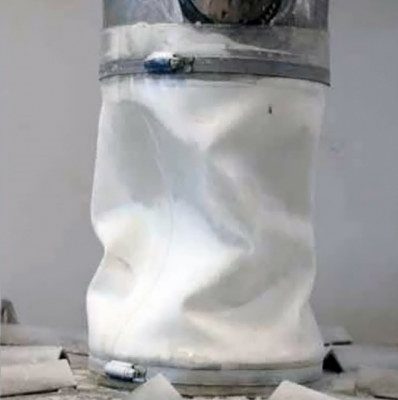
For: traditional cuff with hose clips
|
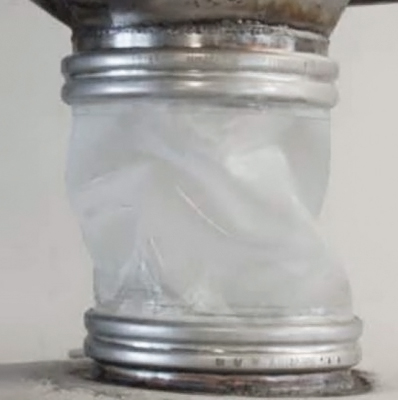
After: BFM fitting
|
The result
Hub Knoren, maintenance technician at AkzoNobel Elotex in Geleen, is enthusiastic about the BFM fitting: "After seeing the first results, I was immediately convinced. This solution is simple and effective. After a few months, the result was clear for all to see: the BFM fitting provided a perfect seal.""
""We are very happy with this solution."”
Want to know more?
Want to know more about the benefits of BFM fittings or specific fittings for ATEX environments?
Download our white paper 'dust explosions and ATEX' or contact us without obligation.
Download the white paper