31-05-2022
|
2 min reading time
Dust reduction with the loading system: the DSH-Hopper
The challenge: curbing dust emissions outside the sheds
Cargo ships bringing cargoes of phosphate regularly dock at ICL's fertiliser plant in Amsterdam. In the past, phosphate from these ships was dumped into sheds via a conveyor belt and a chute from a height of 9 metres. To limit atomisation, ICL dumped with only 30 per cent of its dumping capacity.
Nevertheless, dust remained an area of concern for ICL, for example in terms of visibility in the storage sheds, which restricted operations inside. ICL also wanted to further curb dust emissions outside the warehouses. As Vlint had already been responsible for supplying filters and maintenance of dedusting systems in ICL's factories, offices and laboratories for many years, Vlint was asked for advice.
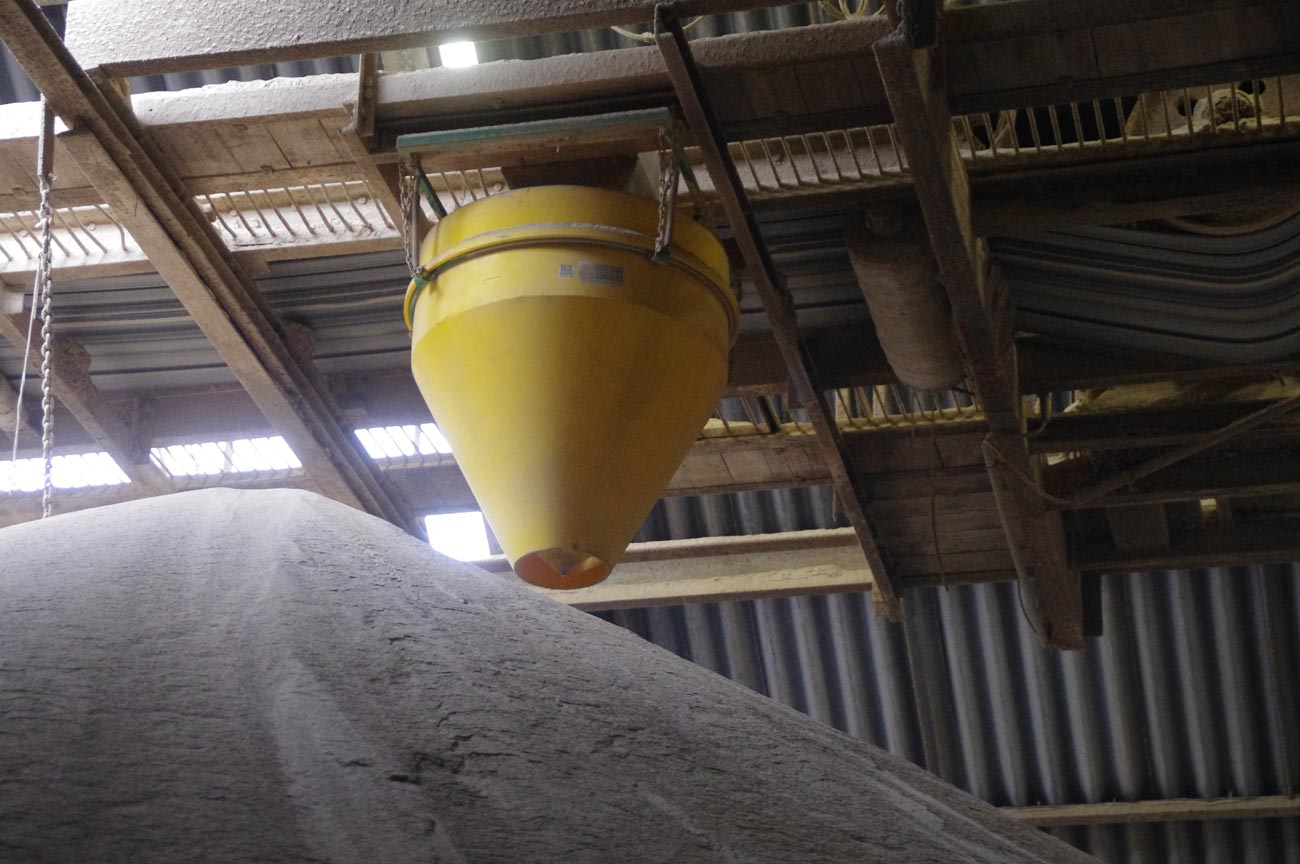
The DSH loading system
|
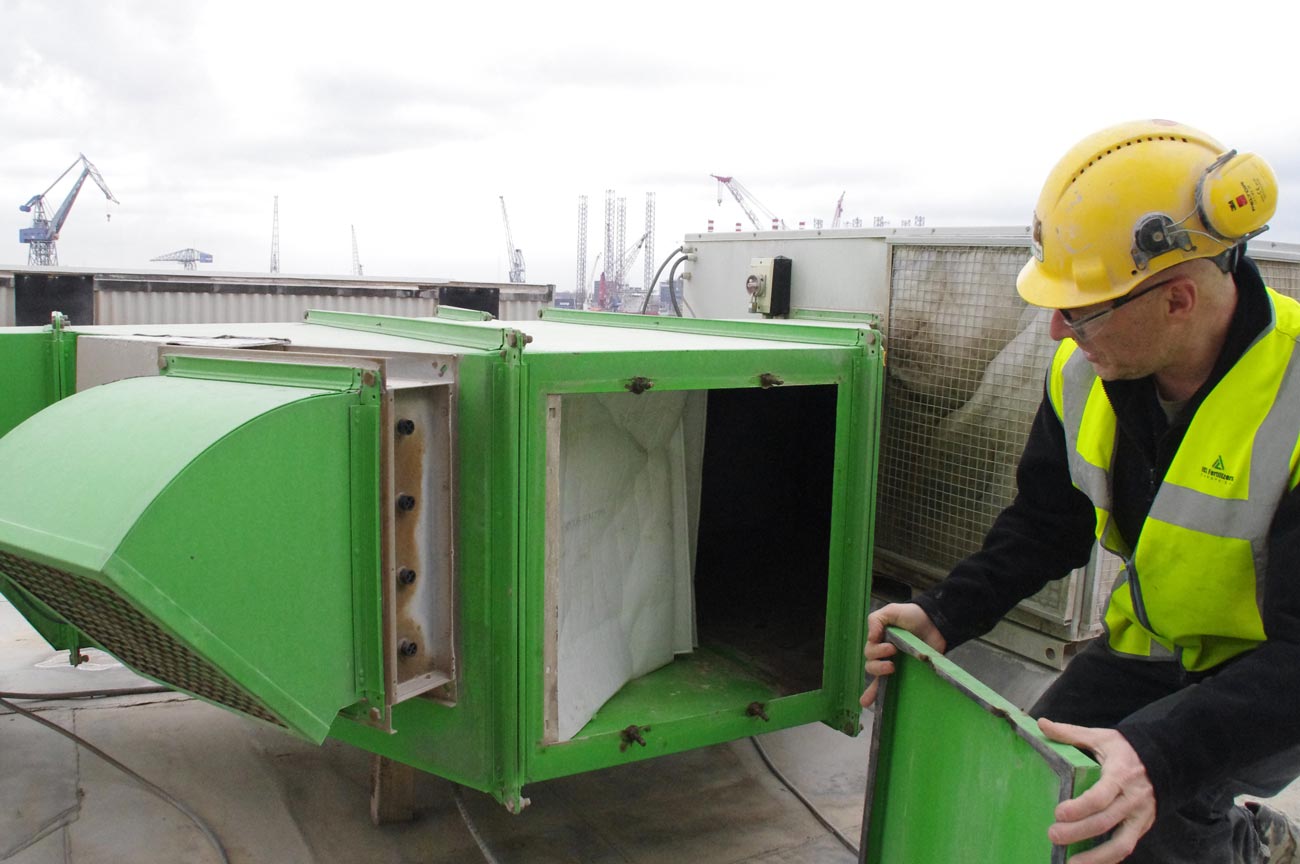
Gerard Oudshoorn
|
"Vlint's product specialist remained in the phosphate-filled shed without interruption to monitor whether everything was going well."
The solution: the DSH hopper
Vlint's product specialists suggested installing a DSH hopper. A DSH-hopper is installed under a feed point such as a conveyor belt, chain conveyor or silo, where it can constantly remain at its operational height. Inside the DSH-hopper is a cone along which solids are guided. In this way, the air is removed from the product, creating a compact product flow that ensures significant dust reduction during loading. Important advantages of the DSH-hopper are:
- Dumping possible up to 20 metres, with minimal atomisation
- More compact dump flow allowing more product to fit in a smaller space
As the DSH hopper has no electronic parts, it is particularly maintenance-friendly. The hoppers are available in polyethylene, stainless steel and hardox, making them suitable for different types of solids (hygroscopic, abrasive, food, etc).
The result: dust reduction and faster loading
With the DSH hopper, ICL now dumps 400 tonnes of phosphate per hour. This is about 60 per cent of the maximum dumping capacity. Because of this operation, the ships in front of the ICL plant are loading much shorter than before. Moreover, dust outside and inside no longer poses any problem.
Gerard Oudshoorn, business office coordinator at ICL in Amsterdam, is extremely pleased with Vlint's advice. He is also impressed by the commitment Vlint's staff showed during the installation. "The loading of phosphate went on continuously for 6 hours during our first tests with the DSH hopper. Vlint's product specialist remained in the phosphate-filled shed without interruption to monitor whether everything was going well. To me, this marks the character of the Vlint specialists," Oudshoorn said.
Process solutions by Vlint
If you are interested in our solutions for your process, we would be happy to help you with tailor-made advice. Or do you have further questions about Solids Handling? Then fill in our contact form and we will contact you within one working day!
or more information, feel free to read through our Solids Handling brochure.
Interested? Get in touch with us