31-05-2022
|
3 min read time
Coffee Company: the importance of clean process air in a coffee factory
"Vlint supplies the right filters for each process, in line with specific requirements, including the necessary certificates, making it an important partner for many companies."
Zaandam is home to one of the largest coffee factories in the Netherlands, that of Ahold Delhaize Coffee Company. It produces Perla coffee (AlbertHeijn's own brand) and own-brand coffee for other retailers and wholesalers in Europe. For almost 10 years, Vlint has been relieving the Zaanse coffee roaster of dust in their production process.
The history of this coffee roaster starts in 1895, when Albert Heijn took over the grocery shop in Oostzaan from his father and started roasting coffee. Since then, the company has continued to grow, serving markets across Europe. The entire process takes place in the factory; from buying and blending to roasting and packaging coffee. Ground coffee, coffee beans, coffee pads and coffee cups, accounting for 19,000 tonnes of coffee annually. That's more than 3 billion cups of coffee!
Air quality
The importance of pure, clean (process) air is high in a factory where coffee is processed from raw beans to finished product. Air quality in a production facility is essential for the quality of coffee products. Indeed, dust particles released in the roastery production process can become airborne and spread through the roastery or production hall, possibly adhering to surfaces or entering equipment, ventilation ducts, gears and clothing.
Unburdening
Vlint has been relieving Ahold Delhaize Coffee Company of the dedusting of their production process since 2011 and has been in contact with Etienne Timmerman, technical maintenance coordinator for this purpose: "I am responsible for the planning of external maintenance engineers for the dedusting installations in the factory, in the roastery and in five halls. We have been working with Vlint for this since 2011. Vlint's mechanics remove and replace dirty filters, clean the section and make a report of the work."”
"Maintenance is always done well and neatly
and the mechanic doesn't leave any mess behind. That's very nice."
Etienne Timmerman knows better than anyone the importance of clean air in a food processing plant. "That is why we check the positions of the filters annually according to a fixed maintenance plan and determine whether maintenance is needed. If so, we contact Vlint, which then sends a technician. This is always a regular mechanic, a skilled type, who knows all the locations of the filters in the plant. The maintenance is always done well and neatly and the mechanic does not leave any mess behind. That is very pleasant."
Bespoke
Thanks to years of experience in dedusting, Vlint's specialists are valued advisors to the (food) industry. Vlint thinks along with you about the safety of the production process and advises food, pharma and chemical companies about the possibilities in the field of food-grade dedusting filters. Bertwin van Gortel, account manager Industry at Vlint, says: "Vlint supplies the right filters for each process, in accordance with specific requirements, including the necessary certificates and is therefore an important partner for many companies." Thus Vlint ensures that the customer does not have to worry about filter-related production stops or recalls. Etienne Timmerman also knows this: "Vlint thinks along with us and unburdens us. We know where to find each other when we need each other. I appreciate that."
Filters and cuffs
Vlint supplies Ahold Delhaize Coffee Company with filter bags, filter folders and filter hoses suitable for the food industry. These filters are made of anti-static polyester/needle felt and are custom-made in the company's own factory by Vlint's professionals. Because these filters are antistatic and electrically conductive, they do not constitute a source of ignition in an explosive environment. In addition, two years ago, on the advice of Bertwin van Gortel, nylon (food grade) cuffs were also supplied for the 25 silos. Previously, rubber cuffs were used in the silos. This rubber became soft due to the greasiness contained in the coffee beans and also gave off colour to the material. "Using cuffs made of nylon - a breathable material - solved this problem," says Bertwin van Gortel. It is an example of how Vlint thinks along with the customer. Etienne Timmermans is pleased: "Bertwin's advice on the nylon cuffs shows exactly why we have been working with Vlint for so many years. Vlint solves it. We are satisfied."
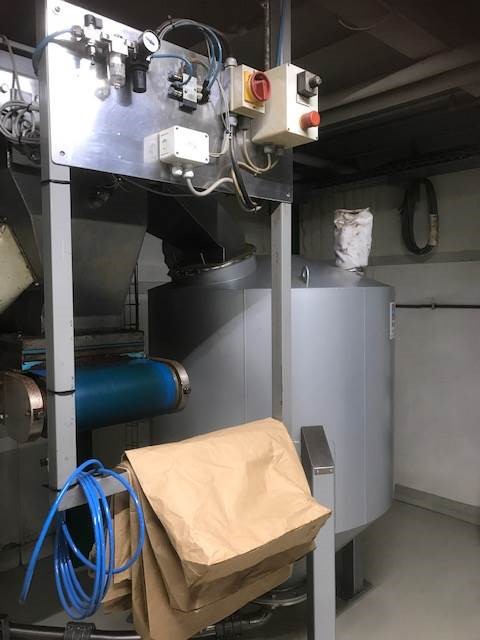 |
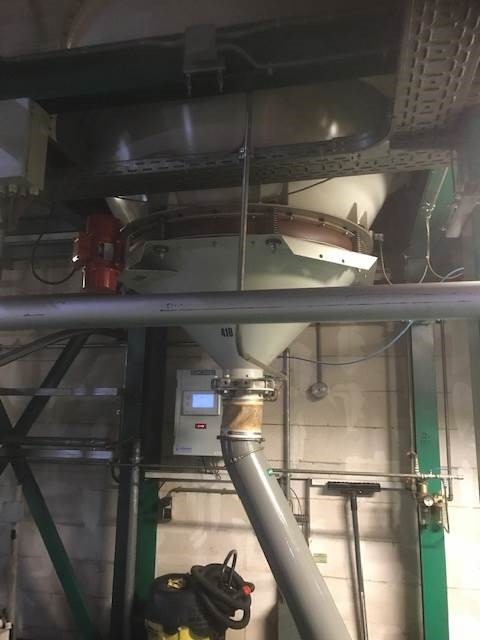 |
Wondering what we can do for you?
At Vlint, we help our clients by first properly analysing the problem. Then, we create and implement an effective plan of action to properly solve the problem. Interested? Feel free to leave your contact details. We will contact you within one working day.
Please contact me/a>